Design for Maintanability / Serviceability w przykładach.
Przedwojenny polski samochód CWS T-1 można było rozkręcić i złożyć tylko jednym kluczem „17” bo wszystkie śruby i nakrętki miały jeden rozmiar. To skrajny przykład myślenia projektanta (był nim ekscentryczny Tadeusz Tański) by ułatwić życie tym ludziom, którzy potem mają taki pojazd naprawiać.
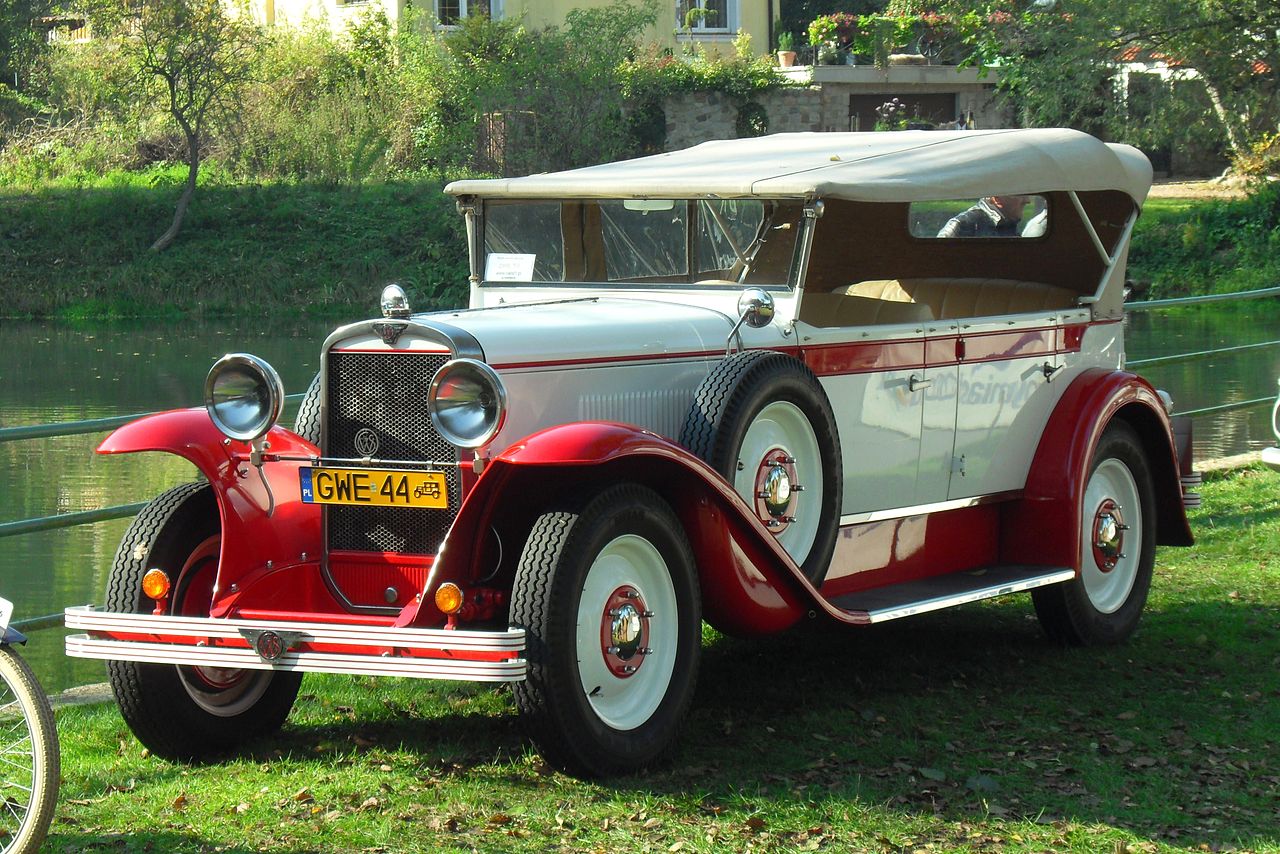
Zdj.1 Replika CWS-T1 w wersji Torpedo, autor zdjęcia Artur Andrzej.
Komisja Europejska w październiku 2019 przyjęła pakiet rozwiązań dotyczących prawa do naprawy, aby zmniejszyć ilość elektrośmieci i emisję CO2. Oznacza to, że od 2021 wprowadzane do obrotu zmywarki, lodówki czy telewizory będą musiały mieć oznaczenie jak łatwy w naprawie jest to produkt.
Podobnie jak dziś porównujemy klasę energetyczną, będziemy mogli porównywać serwisowalność, a producent musi utrzymać dostęp do części zamiennych nawet 10 lat po sprzedaży.
To tylko jeden z aspektów światowego trendu dbania o środowisko. Wpłynie on na pracę konstruktorów bo podobne regulacje wprowadzają także USA. Nowe urządzenia mają być coraz łatwiejsze w naprawie przy użyciu łatwo dostępnych narzędzi. Wygląda na to, że epoka planowego postarzania produktów odchodzić będzie do historii, co sporo zmienia w pracy projektantów.
Najlepsze praktyki w projektowaniu pod łatwy serwis i utrzymanie jest treścią szkolenia Design for Maintanability / Serviceability. Poniżej ten temat głównie od strony użytkowania takich urządzeń.
Na początku 2021 w dyskusji na LinkedIn poprosiłem inżynierów o historie z urządzeniami dobrze i źle zaprojektowanymi pod kątem serwisu. Oto one:
W branży automotive są firmy, które przykładają wagę do servisability i takie, które na to nie poświęcają zbyt wiele uwagi. Toyota dba, aby można było jej auta naprawiać, gdy mają drugie życie w Afryce. Ford, szczególnie w USA, bardzo dba, by samochody były łatwe do serwisowania, czasem robi audyty projektów pod tym kątem, niektórzy nazywają to „Fit for Use”. Mercedes ma specyficzne podejście, bo serwis jest dla niego okazją, aby poprawić w pośpiechu zaprojektowane innowacje. Mistrzem jeśli chodzi o możliwośc napraw w siermiężnych warunkach jest natomiast ...
Łada. A to dlatego, że używa GOSTów - norm państwowych na części. I tak np. wtyczka do lamp i silniczków elektrycznych będzie nie tylko taka sama jak w poprzednich modelach, ale nawet taka sama jak w ... Kamazach. Wygląda to tak, jakby przemysł był podporządkowany wizji kolejnego zjazdu sprzętu na Łuku Kurskim.
Będąc jeszcze na studiach bez namysłu zaoferowałem się, że wyczyszczę komuś wentylator w laptopie (HP pavilion dv5). Potem okazało się, że żeby to zrobić trzeba rozłożyć go na oddzielne atomy. Żeby odkurzyć wentylator (sic!!!). To takie kuriozum, że ktoś w Internecie nawet ułożył o tym piosenkę (poniżej).
Film 1: Rozbieranie dokumentnie całego laptopa HP Pavilon dv5 by dostać się do wentylatorka w żartobliwej piosence (4 minuty). Instrukcja na ifixit.com zawiera 46 kroków by to zrobić.
Pamiętam jak w swojej karierze kilka lat temu miałem do czynienia z oprawami lamp zawieszonymi w magazynie wysokiego składowania. Jeden model do wymiany źródła światła wymagał odpowiedniego rozkręcenia obudowy przy użyciu wkrętaka płaskiego i za chwilę krzyżaka. Szkło oprawy nie miało żadnego zamocowania i po odklejeniu się od uszczelki często spadało, lub wręcz nie można było go zdjąć. Wszystko na podnośniku na 16 metrach. Druga firma używała zatrzasków, szyba miała uchwyt i spokojnie można było opuścić ją po odkręceniu bo utrzymywało ją jarzmo. Oczywiście ten drugi model był ulubiony. Źródła światła były takie same. Modeli już nie pamiętam :-)
Przemyslaw Czapski wskazał na stronę, na której publikowane są niezależne oceny naprawialności telefonów komórkowych.
Najgorszy (1 na 10) jest na dzień pisania artykułu HTC One, najlepszy Fairphone 3 (10 na 10).
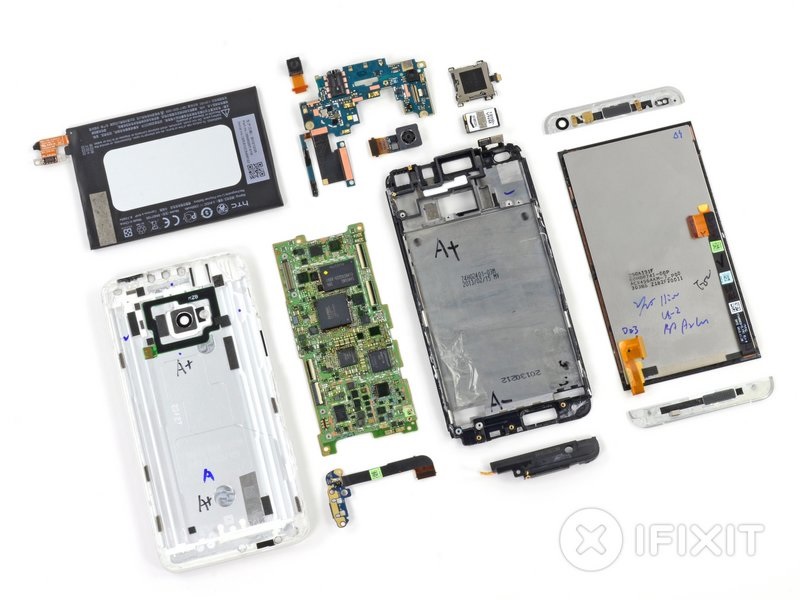
Zdj. 2 Telefon HTC One po dziewiętnastej operacji rozkładania na części pierwsze, na pewno serwisowalność była nisko w priorytetach projektantów, zdjęcie z ifixit.com
Warto też wspomnieć o obecnych samochodach gdzie do wymiany żarówki w niektórych modelach trzeba zdemontować przednia lampę, cały zderzak lub wyjąć akumulator, żeby się dobrać do żarówek. I tutaj chyba nie ma koncernu, który by nie miał tego typu rozwiązań. Ciekawe rozwiązanie w samochodach mają też rozruszniki, które są również dobrze poukrywane między silnikiem, a przednią grodzią i praktycznie nie do wynajęcia bez demontaż silnika (Zafira I).
Dla mnie takim przykładem mogą być dzisiejsze żarówki. Jak się psuje dzisiejsza świetlówka, to musisz wymienić ją całą wraz z elektroniką, gdy w większości przypadków popsuta jest tylko sama świetlówka. Z ledami jest podobnie. Najczęściej zawodzi elektronika, a nie samo źródło światła - dioda LED, niestety zmuszeni jesteśmy do wymiany całości, tworząc przy tym masę śmieci.
Wrył mi się w pamięć mikser planetarny, śruby ze specjalnym łbem, którego zwykłym śrubokrętem nie odkręcisz, łączenia obudowy na zatrzaski wciskane, ale jednorazowe, zębatka z miękkiego tworzywa, która szybko się wyrobiła (zęby się pościerały). Pasek przetrwał, a zębatka już nie.
Zainspirowany podobnym wpisem wskazał na częsty błąd, który popełniają inżynierowie odpowiedzialni za utrzymanie ruchu:
Mógłbym wyciągnąć gitarę i przy kominku śpiewać o tym całą noc... (może to zrobię?) W skrócie. Inżynierowie odczuwający ból przy serwisie mogliby go nie odczuwać, lub nie tak intensywnie, gdyby na etapie odbiorów koncepcji czy 'design freez' konstrukcji byli na spotkaniach obecni lub obecni nie tylko ciałem. To byłoby już czymś, co w historii ludzkości było używaniem koła. ?
To jest idea, którą można sobie wziąć do serca i zastosować od razu.
W swoim poście napisał o pozytywnym przykładzie - pochwalił się projektem, gdzie przez pięć lat nie było ani jednego zgłoszenia serwisowego lub reklamacyjnego. Oto on:
Adapter sondy jednorazowej (medycyna - nakłada się na to jednorazowe sondy, w środku jest gaz pod ciśnieniem) był zaprojektowany dla firmy Metrum Cryoflex pięć lat temu.
Na zewnątrz bardzo prosta konstrukcja, w środku niekoniecznie.
- spawanie laserowe
- zabezpieczenia przed odwrotnym włożeniem końcówek
- oringi zabezpieczające przed przeciekami
- mikro-wkręty zapewniające płynny ruch
- blokowanie ruchu przez mechanizm kulkowy
Do każdego aparatu dodawaliśmy zestaw naprawczy, składający się z zestawu oringów oraz kluczy i gniazd.
Jak miło się dowiedzieć, że przez pięć lat nie było żadnych serwisów i żadnych reklamacji związanych z działaniem.
Miód na uszy inżyniera :)
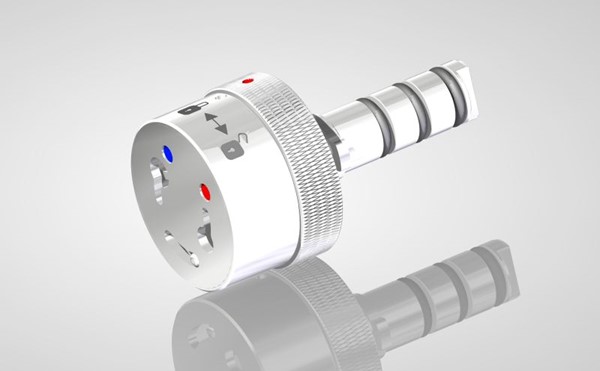
Rys. 1 Adapter sondy projektu Jacka Olszewskiego.
Wojciech Kwaśnicki napisał zaś coś, co może być świetnym podsumowaniem:
To, czym najczęściej denerwują mnie producenci sprężarek powietrza jest wiara, że serwisant ma ręce z gumy i może jednocześnie trzymać wąż spustu oleju i otwierać umieszczony po przeciwnej stronie agregatu zawór. Dobrze jest, gdy w ogóle jest zawór przy spuście oleju, bo pewna znana marka uznaje, że wystarczy korek. A do zlania jest „na żywioł” 30 litrów gorącego płynu. Ma ktoś taką kuwetę? Z resztą - nie wiem czy by pomogła, bo spust jest 8-10 cm powyżej podłogi.
Problematyczne bywają też dojścia do różnych elementów. Nie raz dałoby się to zrobić dużo prościej - zaoszczędzono by czasu i bałaganu. Pozytywne przykłady? Są! Jeden producent stosuje śruby umożliwiające uniesienie bardzo ciężkiej pokrywy. Montuje też śrubę rzymską przy połączeniu elastycznym, które trzeba rozkręcić na czas przeglądu. Bardzo to ułatwia pracę. Maszyny tej firmy bardzo lubię serwisować, bo nie trzeba robić nic na kolanach lub w przysiadzie. W dodatku wszystkie wizjery, manometry, olejowskazy i sterownik można obeserwować stojąc w jednym miejscu.
Design for Maintainability / Serviceability to nie tylko niezawodność i trwałość. To także łatwa diagnozowalność, prostota, standaryzacja i ograniczenie różnorodności części, ergonomia i bezpieczeństwo serwisu.
Bardzo dziękuję autorom za wkład.
Michał Hałas
(który to zredagował)