Oto opracowanie inżynierów Mateusza Bareji i Karola Strzelczyka zrobione w ramach II edycji A.INŻ
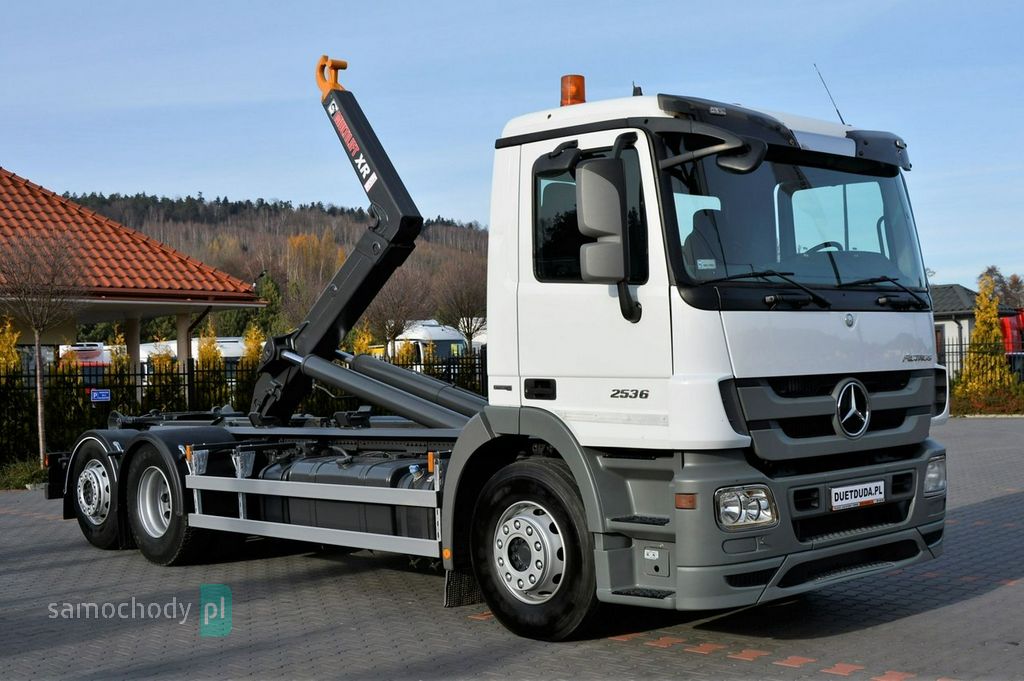
Hakowiec jest specyficznym rodzajem dzwigu,
tu przykładowy, na Mercedesie Actros z portalu samochody.pl
Przed rozpoczęciem udziału w Akademii Inżyniera, zastanawiałem się, co mogę wziąć na warsztat aby przećwiczyć DFA, a może nawet DFM.
Pomysł podsunięty od jednego z kolegów firmy to przeanalizowanie nie znanego mi produktu, a mianowicie konsoli narzędziowej do tzw. hakowców - czyli urządzeń służących do zaciągnięcia kontenera lub platformy na ramę ciężarówki.
Projekt wydawał się bardzo rozbudowany, więc staraliśmy się z Karolem ugryźć go tak, aby móc nad nim pracować w trakcie Akademii.
Jednakże na starcie zostaliśmy obarczeni źle sformułowanym celem: "zrób optymalizację konsoli".
I na tym się skupiliśmy, jednakże wraz z biegiem czasu zaczęliśmy dostrzegać, że sama konsola to jeden obszar ulepszeń, drugi to elementy współpracujące, które także wymagają optymalizacji.
Zaczęliśmy od podzielenia zadania i wybrania 4 ważnych zespołów urządzenia. Komponenty współpracujące z tymi elementami zostały nakreślone jako nie prezentowane - no cóż, pewnych rzeczy się nie przeskoczy.
Poniżej zakres projektu.
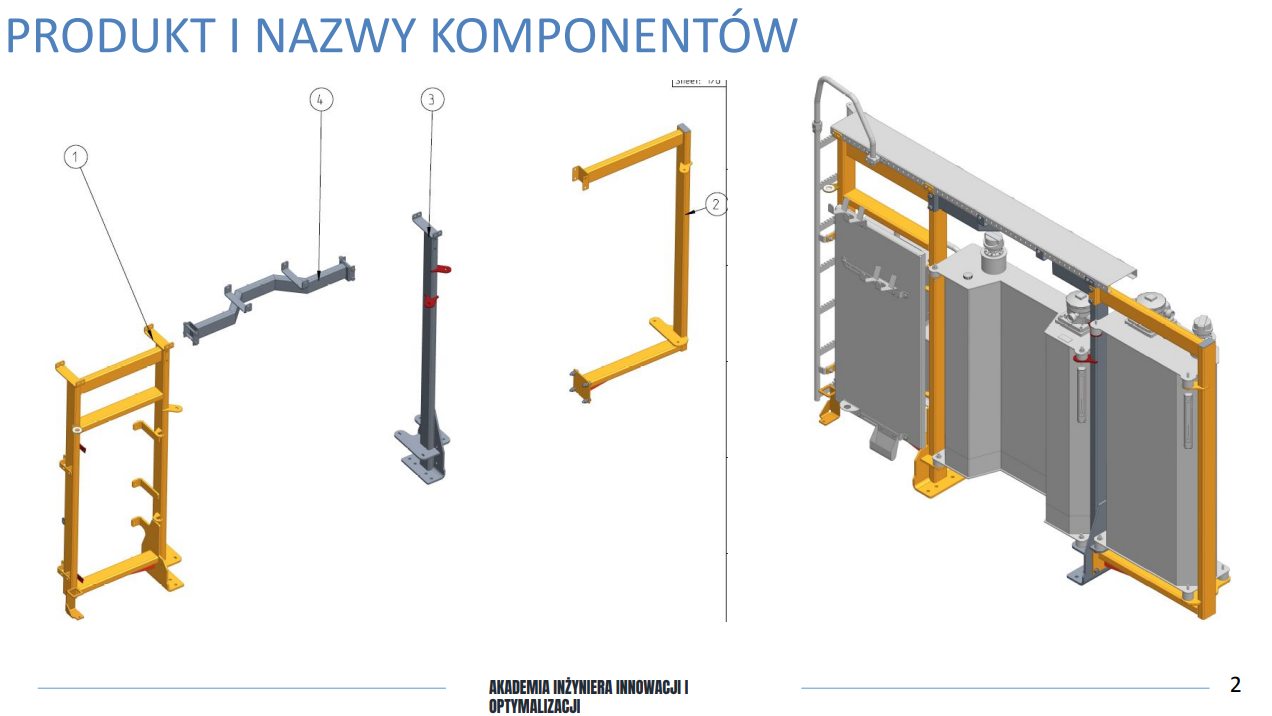
Analizie poddaliśmy wszystkie 4 składowe, jednakże "na warsztat" wzięty został element najbardziej skomplikowany - Rama narzędziowa:


Raport pokazał w czym problem:
- symetria
- metoda
- kierunek
- pozycjonowanie
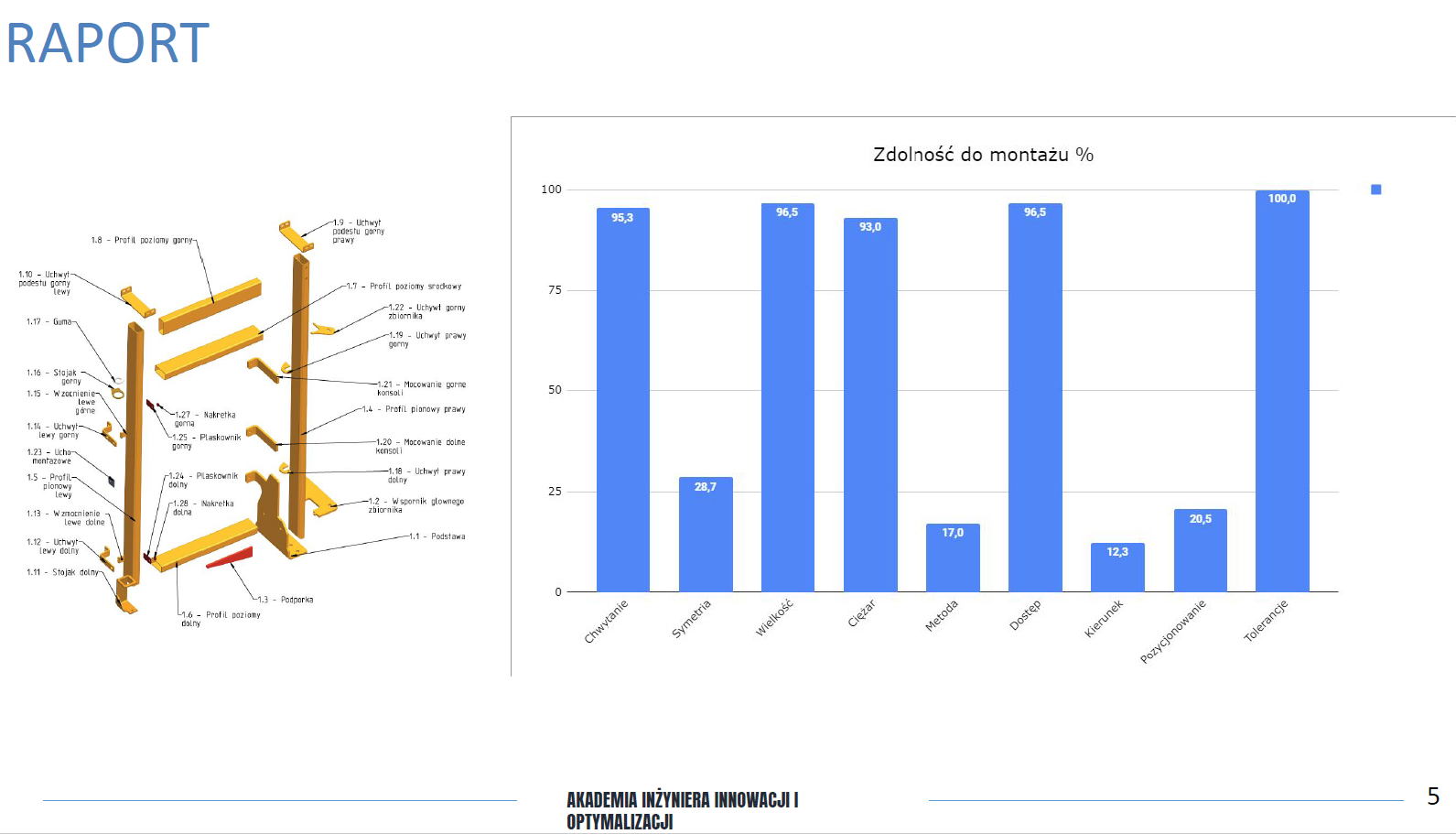
Szczegółowy raport pokazał to dokładniej:
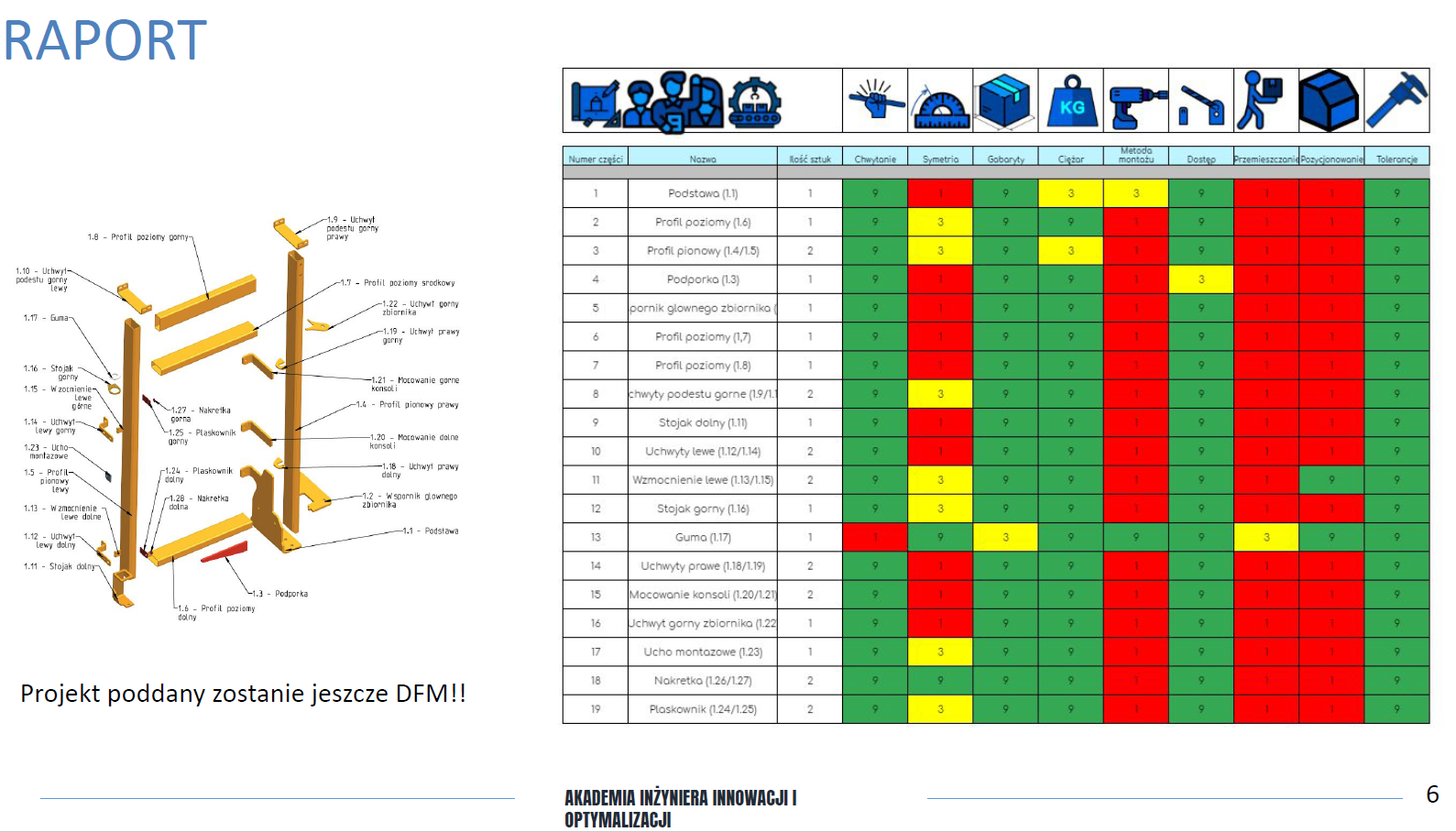
Pomysłów było wiele, ale tyczyły się one wielu obszarów.
- połączenie elementów podporowych jako jedna część,
- zamiana elementów spawanych na gięte - dotyczyło profili
- unifikacja elementów łącznych
- re-design komponentów współpracujących
Rezultatem tego była redukcja modułów z 4 na 3 - to już jakiś postęp.
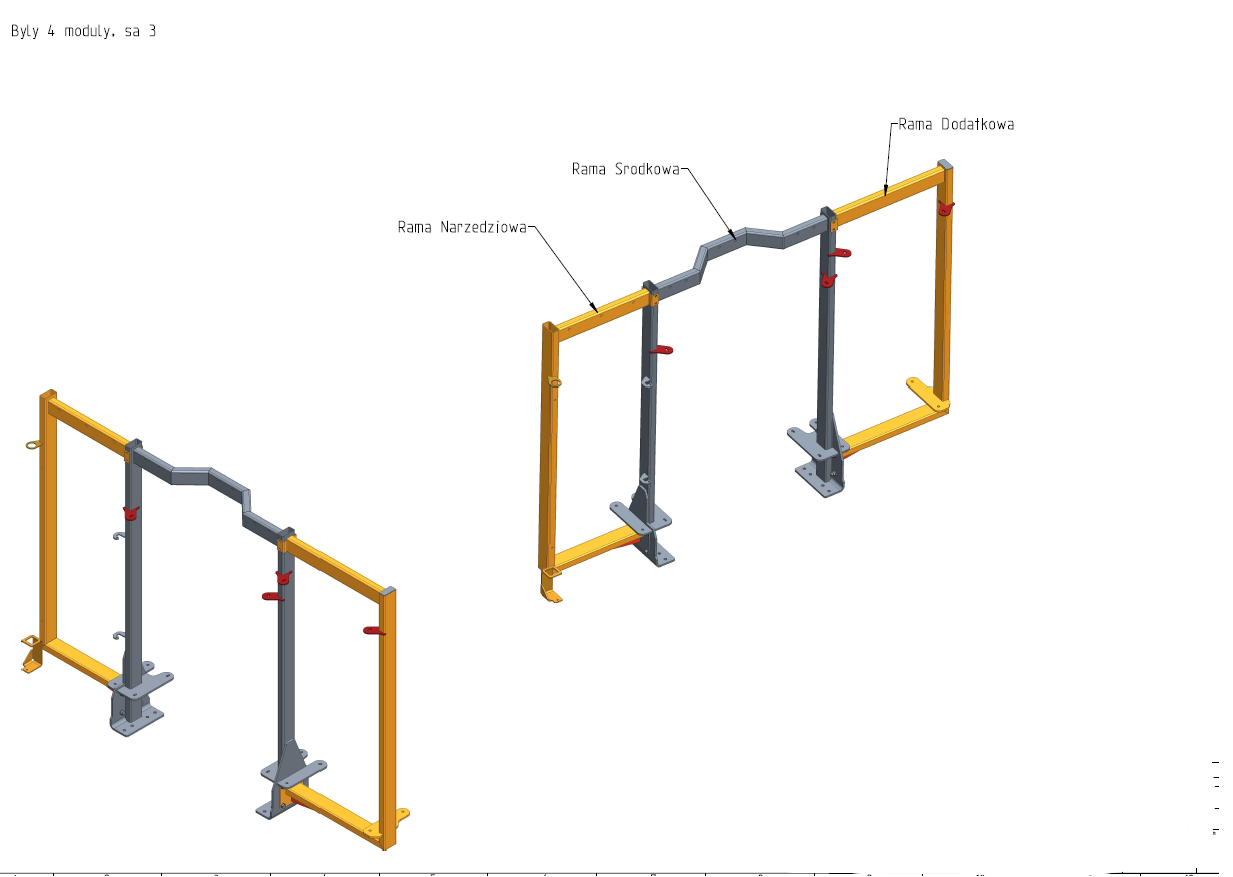
Tak jak wspomniałem wcześniej, przeanalizowaliśmy każdy z elementów a poniżej optymalizacja ramy narzędziowej:
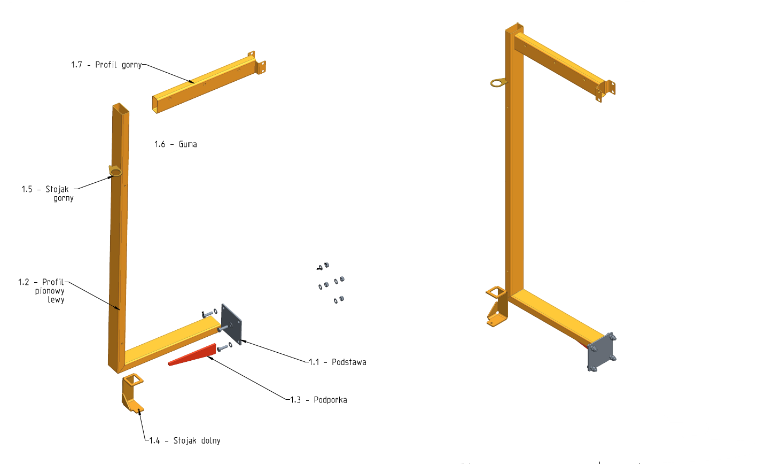
Po ponownej analizie otrzymaliśmy:
Wcześniej było 27 części, teraz jest 7.
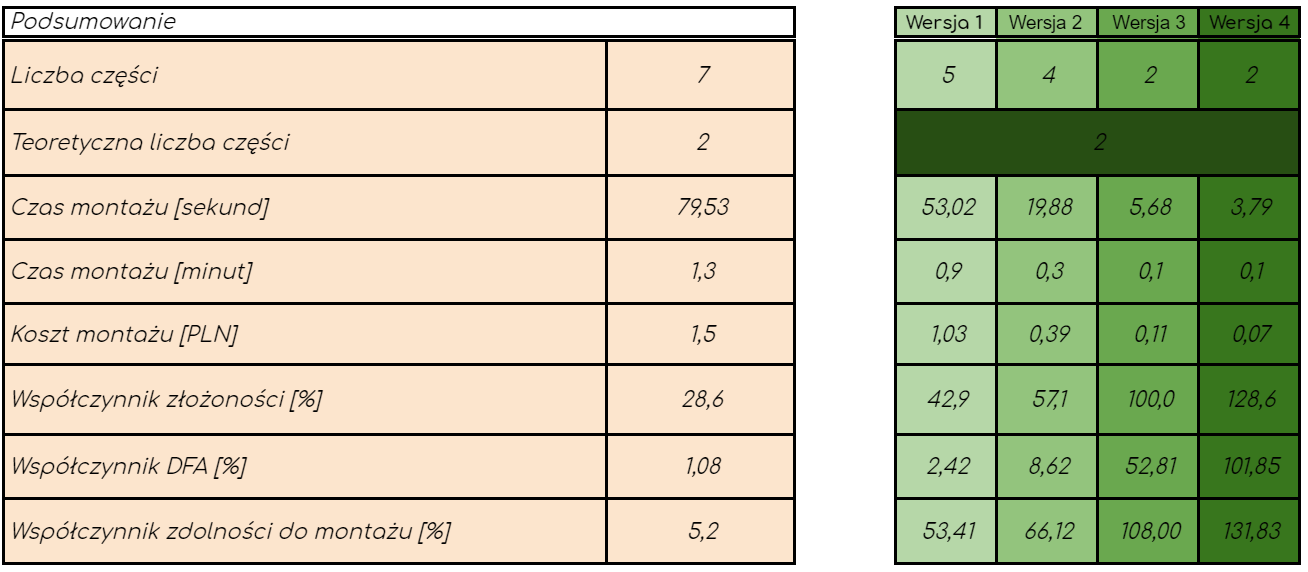
Jak widać dalej mamy problem z symetrią i metodą montażu:


Pierwsze kroki z DFA pokazały, że są obszary, nad którymi jeszcze możemy popracować, jak widać projekt okazał się rozległy, ale już pierwsze rezultaty dają do myślenia.
Poniżej porównanie jak wyglądała konstrukcja na początku, a jak po optymalizacji:
Przed:

Po:
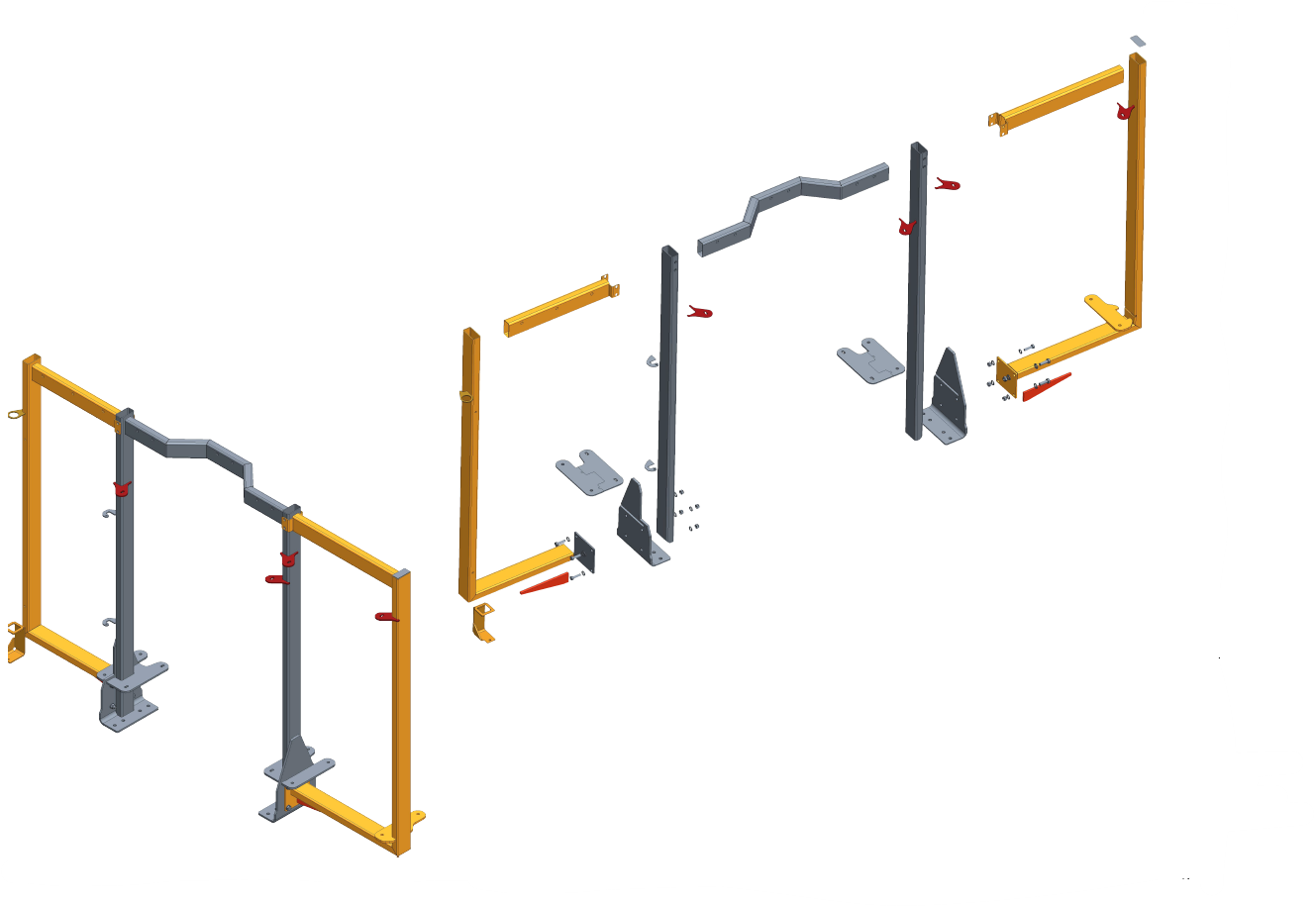
Wstępny szacunek obniżenia kosztu dzięki powyższym zmianom to 15-20%!
Kolejnym krokiem była analiza DFM dla tego zestawu, okazuje się, że taką konstrukcję, można by odlewać jako jeden zespół!!!!
Czyli może być jeszcze taniej, trzeba jednak tą koncepcję dobrze sprawdzić.
Mateusz Bareja
Najbliższe szkolenie Design for Assembly
Następna edycja Akademii Inżyniera Innowacji i Optymalizacji